From Gears to Algorithms: How AI Is Reshaping the Malaysian Manufacturing Industry
Embracing AI Is No Longer Optional but Essential for Survival and Success
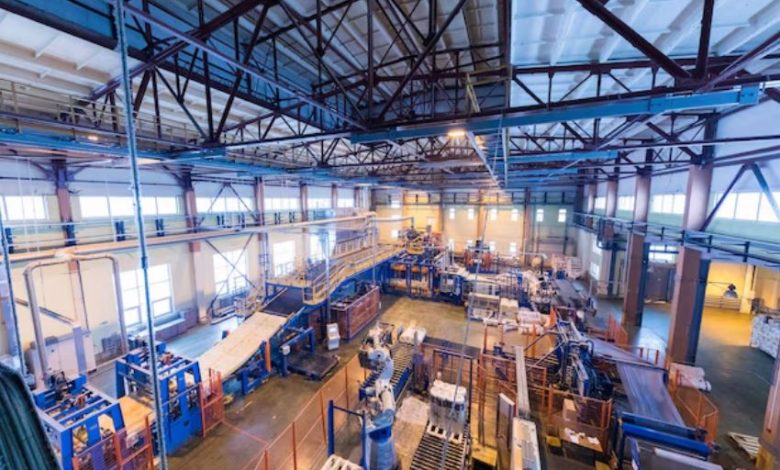
In today’s industrial battleground, the manufacturing industry confronts a crucible of challenges: crushing cost pressures, supply chain chaos, and the unyielding demand for innovation without sacrificing stability or safety.
Meanwhile, the sustainability revolution continues to move forward progressively, mandating slashed carbon footprints and circular economy transformations. The Natural Resources and Environmental Sustainability Minister Nik Nazmi Nik Ahmad urged the private sector and industry bodies to provide leadership and advocacy in their sustainability transition.
He shared that Budget 2025âs allocation for environment and sustainability focused on transitioning Malaysian cities into eco-cities. According to him, by doing so, it would allow more private businesses to adopt and implement sustainability practices.
Amidst such developments, generative Artificial Intelligence (Gen AI) rises as a beacon of hopeâa revolutionary force poised to redefine the very essence of manufacturing.
This cutting-edge technology promises not just incremental improvements, but quantum leaps in process optimisation, efficiency, and groundbreaking innovation, arming manufacturers with the tools to not only survive, but thrive in an era of unprecedented change.
Manufacturing Sector in Malaysia Is Entering a New Frontier
In Malaysia, the manufacturing sector plays a significant role in the economy. The countryâs manufacturing GDP is projected to grow by 61%, reaching RM587.5 billion by 2030, with the electrical and electronics (E&E) industry remaining a key pillar. This growth aligns with the global push for smart manufacturing, where AI, automation, and robotics are increasingly essential for optimising production, including in areas such as electrical components used in various manufacturing processes.
The use of AI-powered high-speed precision industrial robots at its manufacturing facility in Malaysia is a good example.
SMART Modular Technologies (SMART), a global leader in specialty memory and storage solutions, provides a shining example with its use of AI-powered high-speed precision industrial robots at its Malaysian facility. SMART has implemented IBM Maximo Visual Inspection to identify and isolate manufacturing defects, reducing the likelihood of non-compliant products being shipped to customers.
Integrating quality control automation into their manufacturing process allows for defect visualization and early elimination, enabling SMARTâs operation the opportunity to be highly efficient, predictable and to uphold higher quality standardsâgiving new meaning to âsmart Malaysian manufacturingâ.
As manufacturing moves toward greater automation and digital integration, electrical distributors supply advanced technologies that facilitate real-time monitoring, predictive maintenance, and optimised energy use, key for digital transformation.
The electrical distribution industry, supplying essential parts and technologies to manufacturing firms, also plays a vital role in driving the sectorâs transformation towards more efficient and digitally integrated operationsâ.
Another good example is KVC, a Sonepar Company, a leading B2B distributor of electrical products, solutions, and related services, leveraged IBM Robotic Process Automation (RPA) to enhance the Finance department’s Procure-to-Pay process by significantly improving operational efficiency. IBM RPA reduces errors and lowers costs by automating key tasks such as invoice extraction, matching, and payment processing. This streamlined approach accelerates workflow and ensures more accurate and timely payments, driving better overall financial management.
Additionally, KVC also leveraged IBM Decision Manager to help the company improve its credit evaluation, extension, and approval process by automating key steps. The system downloads CTOS reports, integrates them with the internal credit scoring matrix, and generates recommendations for credit line adjustments or duration extensions. It also automates approvals, streamlining operations, reducing manual intervention, and enhancing speed, accuracy, employee productivity and customer experience.
AI and Gen AI have transformative potential for asset management, sustainability, and manufacturing processes. However, unlocking this potential requires more than technological investmentâit demands a shift in mindset, a reimagining of traditional processes, and a commitment to continuous learning.
For industry leaders ready to innovate, the rewards are substantial: greater efficiency, enhanced sustainability, and improved competitiveness, empowering them to navigation through an increasingly complex business environment with confidence.
As we enter a new era in manufacturing, the imperative is clear: embracing AI is no longer optional but essential for survival and success in todayâs industrial landscape.