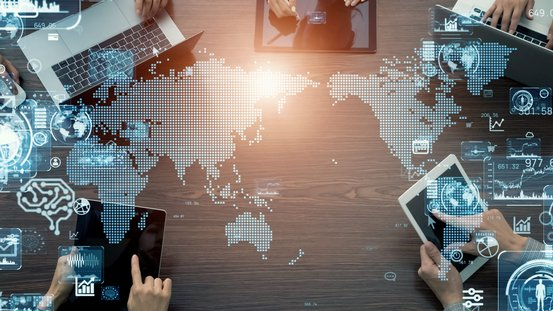
Challenges are nothing new to manufacturers.
And, over the past three pandemic years, businesses in the industry have had to face supply chain-related problems that have only highlighted the sometimes fickle nature of manufacturing—along with the need to find transformative solutions that can help in addressing these challenges.
At the same time, manufacturers are also looking for ways to enhance their operations to mitigate the impact of labour shortages and to adapt to what is becoming an increasingly complex and competitive manufacturing landscape.
Manufacturers are responding accordingly, and one way they are doing so is by turning to technology.
In particular, more and more manufacturers are striving to be more data-driven, says Tim Long, Global Head of Manufacturing at Snowflake. All the while, companies are continuing to leverage technologies such as Artificial Intelligence (AI) and Machine Learning (ML) “for visibility and insights into performance to create leaner, more sustainable and cost-efficient supply chains.”
Data Is a Differentiator
Put simply, data is power in the manufacturing sector. It can drive businesses forward.
“Data is crucial in helping manufacturers efficiently deliver the best products possible, focusing not just within the factory but end-to-end—from product design to post-sales service,” Long explains. “Analysis of product performance and usage information enables organisations to identify defects and tailor goods according to the customers’ needs.”
Long cites as an example the case of truck, bus and industrial engine manufacturer Scania, which leveraged a modular data mesh approach to create custom hardware and service solutions to adapt to different situations. According to Long, Scania was able to drive customer personalisation and shift towards more sustainable and efficient transport solutions without raising costs or hampering productivity because it was equipped with high-quality connected vehicle data.
More importantly, data can help manufacturers address—or at least mitigate—supply chain problems that commonly hamper production.
“Access to high-quality data is crucial in providing organisations with a window into their supply chain performance. Insights gathered from IoT devices or sensors can help organisations identify issues and improvement areas to maximise their efficiency,” Long points out. “Additionally, organisations can tap into third-party data to monitor the broader ecosystem for risk and disruptions.”
To this end, Long cites as an example Fortune 100 company Honeywell, which is using Snowflake’s Manufacturing Data Cloud to store and analyse all of its enterprise data. In doing so, it is able to optimise its supply chain and drive dynamic pricing for as many as 3.5 million SKUs globally—in turn helping the company preserve its status as among the world’s most reliable manufacturers of safety and productivity materials, aerospace parts and building technologies.
Data Siloes: Barriers to Data-Driven Leaps Forward
Despite data’s primordial role nowadays, quite a few manufacturers are still unable to make the most out of their data, thus hindering innovation and keeping them from responding quickly to volatile market factors and fluctuations. And part of the problem here is the prevalence of data siloes due to legacy systems.
“Legacy workflows that perpetuate silos run counter to the objectives of incorporating data into almost every aspect of the manufacturing process, from the factory floor to the entire supply chain,” Long notes. “Having the data to take visibility to a granular level is critical to improving daily operational performance as well as tactical and strategic decision-making aimed at long-term targets.”
In short, organisations need to implement smart manufacturing best practices that can enable them to break down these data silos so they can unlock the true value of the data they possess.
Enabling and Harnessing a Strong Data Foundation
One best practice today’s manufacturers need to be implementing soon is to establish a strong data foundation—one that consolidates all information collected from different sources under a single, secure pane of glass so it can be analysed to yield useful, accurate insights that can be used for informed decision-making.
That is, incidentally, something Snowflake can help with through its Manufacturing Data Cloud. This platform, according to Long, empowers companies in the automotive, technology, energy and industrial sectors with data “to create leaner, more efficient supply chains and build smarter operations.” Aside from building a strong data foundation, companies using Snowflake’s Manufacturing Data Cloud can take advantage of the wisdom of industry-leading manufacturing partners to enhance solution innovation and shorten time to value.
Together, these capabilities can help manufacturers improve and optimise supply chain performance, where seamless data sharing and collaboration among partners, suppliers and customers will enable the company to gain a complete view of its entire supply chain. In doing so, the organisation will then be able to identify problem areas that need to be resolved and act on them immediately. Paired with SQL capabilities and the Snowpark developer framework, users can even build advanced AI and ML models to activate critical use cases, including forecasting demand, inventory optimisation and transportation efficiency.
In addition, the same platform enables native support for semi-structured, structured and unstructured data across various devices and machines, allowing manufacturers to operate smarter and deliver better outcomes. For instance, real-time shop floor data can determine future maintenance needs, process time, product yield and quality and their sustainability journey. Organisations can then use this information to repair faulty machines, predict quality, identify the root cause of yield issues and scale operations as needed.
Adopted by the Biggest Companies in the World
It’s not for nothing then that Snowflake’s Manufacturing Data Cloud is now being used by some of the world’s largest organisations, including ABB, Électricité de France (EDF), and Molex.
“As a technology leader in electrification and automation, ABB accelerated modernisation to unlock end-to-end business insights and become a more data-driven enterprise,” Long noted about ABB’s use of the Manufacturing Data Cloud. “By unifying its data via the Snowflake Manufacturing Data Cloud, the company leverages actionable insights on incoming raw materials from suppliers, plant production capabilities, and sales orders. This was crucial in helping them streamline their operations and meet customer demands.”
“EDF, the largest energy supplier for homes and businesses across the UK, also relied on our Snowpark Python development framework to build an ML platform in a few months. It made delivering data-driven products easier, which, in turn, boosted customer satisfaction and retention,” Long added. “Molex, on the other hand, turned to our Manufacturing Data Cloud platform to enable digital transformation use cases, like sharing data securely across internal teams and external partners and maximising manufacturing shop-floor and business KPIs.”
Driving Towards Digital Transformation to Meet Consumer Demands
Ultimately, successful manufacturers, according to Long, are those who can meet demands quickly and efficiently. And therein lies the rub.
“Traditional infrastructure simply isn’t capable of keeping up [with the demands of modern-day consumers],” Long explained. “It makes a consistent, integrated view of intra-agency and cross-agency, structured and semi-structured data an impossibility, hindering the organisation’s ability to quickly pivot in the face of challenges or new opportunities.”
Moving past legacy systems, therefore, is the key to meeting consumer demands quickly and efficiently, and that requires manufacturers to embrace Industry 4.0 innovations. In doing so, they will be able to deliver the best quality products in the most efficient ways possible. An example of this, Long says, is the use of AI and ML to predict optimal equipment maintenance schedules based on enterprise and shopfloor data.
Put simply, it is time for manufacturers to be data-driven and embrace digital transformation—as long as both are strategic and tailored to business goals. In this way, companies will be better positioned in terms of driving customer satisfaction, boosting competitiveness and meeting challenges.